Q: The holes at the axle beam ends for the lower ball joint posts on both sides have horizontal scoring, is this common?
------------------------
Totally agree, this is a big job; 4th weekend running (this one 4 days w/Columbus Day!)
----------
If tackling the Dana 44 differential, watch this video (This would be a Dana 50, but otherwise its the same set up):
At time 2:10 I didn't do that; 2:20 didn't do that either :-/ 2:55 did do that!
Pay close attention to the part about leaving a side bolt in until ready to bring the carrier down. I placed a floor jack below the diff, raised to the height of the bottom of the diff, then removed all the bolts thinking the RTV would hold until I got around the back to pull it down. Nope, the RTV lasted about 12 seconds and the diff dropped off the axle beam - right into the cradle on the floor jack. Stupid and lucky. Leave in one of the side bolts!
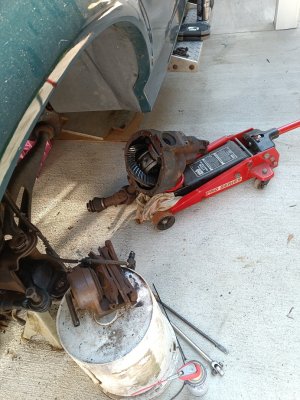
Moved the unit to a table, pulled the axle shaft clip (two screwdrivers to push off the shaft, then rotate and remove with needle nose pliers) and removed the right inner axle. Cleaned and painted the diff carrier (left the vent tube in place), replaced the seals, flushed out the internals with almost a full a can of brake cleaner, then sprayed with WD-40 before any moisture could attack the metal. There was a good bit of residue in the bottom of the carrier. Everything looked good though.
Replaced the U-joint on the inner axle shaft (Non-Greasable Spicer Life DANA 5760X - also at the wheels). Painted the axle shafts gray. Installation is the reverse of removal, as they say. The axle clip took some pressure to re-install, I used the handle end of a pair of clippers that was coated in rubber so I could press it into place and not have the tool slip.
Went with a LubeLocker gasket (also have one on my Jeep XJ-highly recommended).
The alignment pin idea failed miserably, muscling the diff into position knocked out the pins and dropped the gasket out of place.
I managed to get one side bolt in to hold the diff, then fiddled and adjusted for an hour to get the gasket back in place.
Then I was able put all the bolts in by hand, nice and smooth, torqued it up and added 80W-90 Valvoline Gear Oil - which immediately ran out of the left axle hole - Doh! Wiped that up, no other leaks - Victory!

Of course, I knocked off one of the drive shaft U-Joint cups and had to find all the little pin bearings, clean and reassemble.
Pressed the new ball joints into the steering knuckles, next up are the spindle rebuilds and hub bearing replacements.
I just hope this bucket holds up until I get the wheels back on!
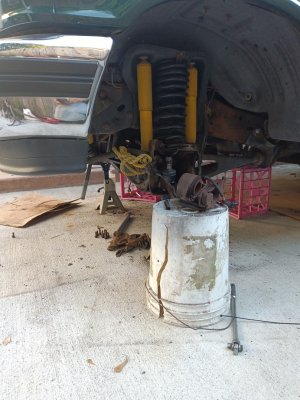