Motech
Well-known member
You can test that back pressure before you go cutting and gutting on a whim. Find yourself an 18mm threaded fitting, same as old spark plugs, something you can thread into a hole and then attach a gauge to.It is the complications with proper exhaust back-pressure and scavenging that make me think that gutting the converter might not serve my purpose. My purpose would be to restore performance to normal and not for any new gains. I'm thinking that my converter is restricted and hurting performance but don't know for sure. The truck only has 46000 miles on it but it was running badly with a dead MAP sensor when I got it and I don't know how long it ran badly and if that could effect the converter.
An old 18mm compression tester adapter works real well, like this one, part of a testing kit or cheap by itself at most any auto parts store.
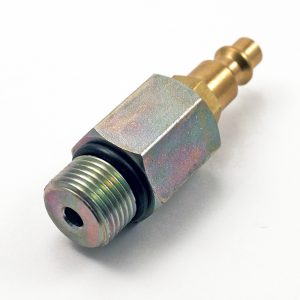
Or even the big-threaded hose of a compression testing set. Just remove the Schroeder valve (just like a tire valve stem) and fit the gauge hose over that instead.
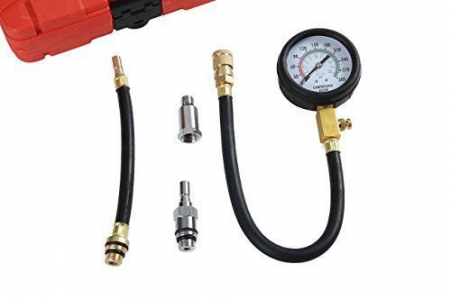
And your basic vacuum testing gauge like this one:
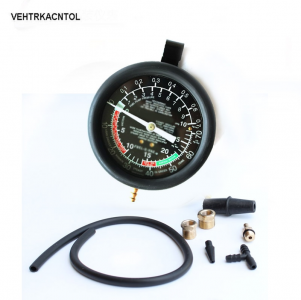
Remove oxygen sensor, thread this in it's place and attach gauge to it with a tight fitting hose.
Fire it up, stabilize, then hold it at 2000 RPM and record your pressure. I say zero, industry says 3 psi max.
Then give it a couple of quick but deep Wide Open Throttle snaps to the floor--let that mill spin quickly up to 4000K RM+PM at least--and note your peak pressure. I say 3 psi max, industry says 5-8, but those levels, 5 psi is robbing power you might not notice til you corrected it, but 8 psi is getting your mill into slug range.
When plugged cats really start to cause power loss grief, pressure will peg these 10-12 psi gauges at WOT snap. That's when engine will be falling on it's face.
(Perfect little homemade example kit)
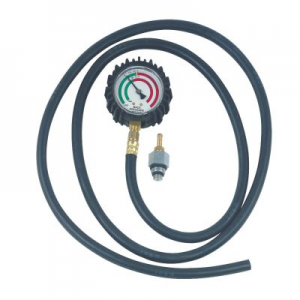
Last edited: