Yo ABE,
Hopefully, other members can assist you soon.
For now;
From Ford:
"Section 01-01: Underbody | 1996 F-150, F-250, F-350, F-Super Duty and Bronco Workshop Manual |
ADJUSTMENTS
Welding
CAUTION: Disconnect the negative battery cable before using any electrical welding equipment.
Perform all welding using Rotunda MIG Wire Feed Welder 164-R3665 or equivalent, and welding wire meeting AWS-E-70S specifications or equivalent.
When performing oxyacetylene welding or brazing, protect the adjacent areas with heat insulation compound.
Because more extensive panel deformation results from oxyacetylene welding than from MIG welding or spot welding, perform sectional welding using MIG welding or spot welding equipment only.
Perform spot welding operations in locations that are inaccessible with spot welding tongs using the hole weld method. Drill or punch 5mm (0.2 inch) holes in one side of the ****** and weld and add filler material.
Varying factors determine plate thickness, panel design, cross-sectionals and sizes, joining method, welding method, and welding locations during manufacturing. To apply the most suitable repair method, therefore, it is most important to completely understand the body design, concept, and construction.
It is essential that repair welds, particularly on load-bearing parts or parts contributing to the strength of the assembly, are equivalent to the originals in size, type, and strength.
Steel Components, Low-Alloy
CAUTION: Disconnect the negative battery cable before using any electric welding equipment.
Because of associated high heat buildup, do not use oxyacetylene when welding high-tensile or high-strength, low-alloy steel components. Use spot, MIG or arc welding. During MIG or arc welding, use a temperature-indicating crayon to make sure that the temperature does not exceed 750°C (1400°F).
- Replace spot-welded components by spot welding where possible. If spot welding equipment is not available, or if the location is not accessible, puddle weld the panels.
- Use MIG welding rather than conventional arc welding when welding high-strength, high-tensile, or conventional mild steel. Use 0.8mm or 0.9mm (.031-inch or .035-inch) diameter wire and conform to Classification AWS A5. 18-69, E70S-6 or E70S-4. MIG welding is also known as GMAW (Gas Metal Arc Welding).
- Perform conventional arc welding using 2.5mm (.098-inch) diameter rods conforming to Classification AS 1552-1973, E4841 or AWS A5. 1-78, E7014.
When cutting salvage or repairable components, use a grinding disc, air chisel, or metal cutting saw.
All welding should be done with a Rotunda MIG Wire Feed Welder 164-R3665 or equivalent, with welding wire meeting AWS-E-70S Specification."
Mickaila's Big Bronco Build:
MIG welder
"For my Lincoln Electric, this is the perfect setting for sheet metal work---with 35 CFM of Ar/CO2.
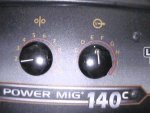
82 XLT Lariat, 351W, C6, NP208, 4.56:1, 37x13.5s, all sheet metal is now replaced!
As with most, I am tired of paying someone to do a patch panel on the quarter panels, complaining about my tailgate, and using fender flares to hide my rust on the front fenders. As such, I am replacing them.
I started with a full site search, which revealed many useful threads:
1. Body work in general:
http://fullsizebronco.com/forum/showthread.php?t=84272
http://www.fullsizebronco.com/forum/showthread.php?t=123743&page=4
http://www.fullsizebronco.com/forum/showthread.php?t=90256&highlight=rear+quarters+sixlitre&page=2
2. Quarter panel replacement:
http://www.supermotors.net/vehicles/registry/4970/19605
3. Flag mount mirrors:
http://www.supermotors.net/vehicles/registry/2742/12641
4. Tailgate knowledge:
http://www.supermotors.net/vehicles/registry/2742/12689
5. Door alignment:
http://www.fullsizebronco.com/forum/showthread.php?t=87752
5.5 Hood, Door and Fender alignment:
http://www.hotrodders.com/forum/aligning-hood-139169.html?highlight=hood+alignment
6. Paint questions:
http://www.fullsizebronco.com/forum/showthread.php?t=143778
Before shots:
This was after taking off the bushwhacker flares--I wonder if the rust here was exacerbated by the flares or if it was just natural course?
In the process of removing:
Some spot welds put up a better fight then others :}
My A-pillar turned out to not be connected by anything more then seam sealer--facilitating this step. I did however have to use the angle grinder to connect the dots
After Driver's quarter was removed:
If you look real close you can see the electrical connector that causes the dome light to fail
Obviously, I will be replacing this inner wheel tub--an advantage of having as much rust as i did, is that i didn't have to drill out any spot welds to the fender--just the ones for the inner tub
After grinding / sanding / sweating the rust off:
There is a spot or two of underbody coating left, but the majority of the metal is bare. It is just an odd angle that makes this appear not fully sanded
After painting with 3 coats of POR 15
I still have a few spots of body work to do in this shot---just covering up the fresh bare metal:
Where we go one, we go all."
●